Pavletic’s unique craft is done using
vintage power hammers. The two main machines stand nine feet tall and
have dies for creating the various shapes found in each part.
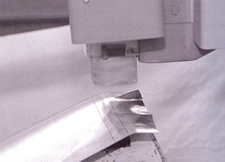
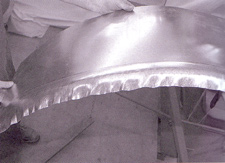
Starting with the old or damaged piece, a sweep gauge can be used to find
the exact shape in the part. Pavletic measures, then makes a pattern before
cutting out the blank piece, compensating for shrinkage.
In fact, he literally stretches and
shrinks the metal to obtain the desired shape. Working back and forth between
stretching, shrinking and test fits, Pavletic eventually gets the shape
he wants. . . .changing the dies in the machine for each task. He usually
uses the same type and gauge of metal as the original.
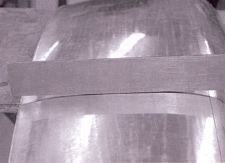
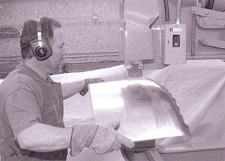
It’s fascinating to see how Pavletic takes flat metal material and shapes
it by hand into an exact replica of the original damaged or rusted piece.
Once it’s
shaped, he rolls the edges if necessary, alternating between stretching
and shrinking. Material that has been formed with the Pettingill power
hammers
is less brittle than their counterparts using shrinking dies.
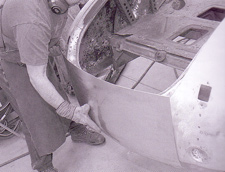
Sometimes, when the original piece is extremely rusted or damaged, Pavletic
finds he needs to trust his eye more than the original. During the entire
process, Pavletic continually goes back to the original to test fit.
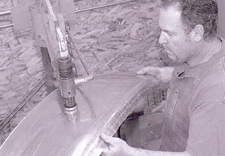
Finishing touches are done with a planishing hammer. The planishing hammer
takes out low spots left by the power hammer. During this, there are still
test fits and comparisons to the original. Again, Mike uses his eye to
create the right crown, because it’s impossible to know the integrity of
the original.
After trimming with a hand snips, Pavletic creates the fold. The tool used
for this depends upon the metal being shaped. Aluminum is soft enough to
use a hand pliers to create the fold. Steel would require a score using a
die on the Pullmax.
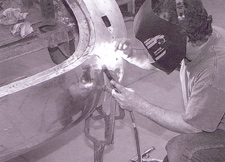
Before welding, Pavletic once again checks the fit, measures the piece against
its older counterpart and flattens the fold. The edges are deburred, cleaned
with acetone and then begins welding with a TIG welder. Many times,the welding
is tricky, especially on older vehicles on which the original panels have
become thin.
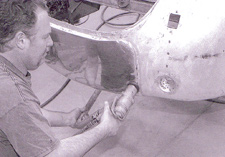
Since the welding causes some distortion, all pieces have to be finished
in place. Pavletic likes to leave the metal as thick as possible and avoids
filing, which can damage the integrity of the metal. Final finish is done
using a pneumatic air-planishing hammer.
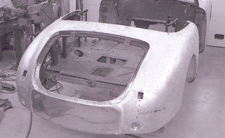
The finished piece on an Alfa Romeo that’s being restored.
All photos on this page courtesy of Tim Remus of Wolfgang Publications. |